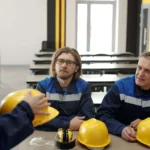
Building automation is no longer just a future concept, it’s happening now. As more building owners embrace electrification and smart systems, electrical contractors have a major opportunity to grow. But there’s a skills gap, and staying competitive means learning automation, data, and AI. With the right training and tools like Raiven, contractors can lead the way in building smarter, more efficient spaces.
Procurement doesn’t have to be a slow, manual drain on your business. With automation and AI, contractors can streamline tasks like purchase order creation, invoice matching, and supplier tracking—cutting costs and boosting efficiency. Raiven’s digital supply chain network makes it easier than ever to build a modern, connected buying process for the trades. Small improvements add up fast, and the impact on your bottom line is worth the effort.
Key takeaways: With so many contractor groups offering similar networking and industry resources, it’s critical to stand out. The most successful organizations are rethinking their value propositions, delivering perks that directly solve electrical and HVAC contractors’ toughest challenges. Below are some high-impact benefits you can offer to attract, support, and retain members in today’s competitive […]
The EV charging market is poised for explosive growth, with over 28 million charging ports needed in the U.S. by 2030. For electrical contractors, this shift presents an opportunity to expand into residential, multifamily, fleet, and public sector installations—along with long-term revenue from maintenance and repairs. Local demand will vary, so understanding your market is key. Raiven’s Electrification Store helps contractors stay competitive with access to discounted supplies, streamlined procurement, and new revenue opportunities through their e-store program.
With up to 48 million American homes needing electrical panel upgrades, the demand for skilled contractors is surging—driven by aging infrastructure and the rise of electrification. Commercial buildings are also due for panel replacements as energy needs and safety standards evolve. To succeed in this market, electricians must communicate value, navigate cost objections, and streamline sourcing. Raiven helps contractors stay competitive with smarter procurement tools, pre-negotiated pricing, and access to high-quality electrification supplies.
Fragmented procurement across multiple locations can lead to overspending, inefficiencies, and compliance risks for contractors and enterprises. Centralizing your buying process helps enforce purchasing policies, reduce costs, and unlock better visibility into spend and inventory. It also makes it easier to adopt tech tools like automation and analytics for smarter decision-making. Raiven’s centralized Marketplace gives your team everything they need to streamline procurement while maintaining flexibility for local operations.
Inaccurate quotes can damage client trust, eat into profits, and create costly rework—but most mistakes are preventable with the right systems in place. Common issues like outdated pricing, poor scoping, and misaligned supplier lead times can all be addressed through process improvements and better tools. Raiven helps contractors quote with confidence by providing real-time pricing, accurate lead times, and a digital supply network to streamline procurement. A solid quoting process protects your margins and sets every project up for success.
With 87% of fleet managers planning to add EVs in the next five years, demand for reliable fleet charging solutions is on the rise. Unlike residential setups, fleet charging requires centralized infrastructure or coordinated at-home installations—creating major opportunities for electrical contractors. By offering smart installation strategies and long-term support, contractors can tap into this fast-growing market. Raiven helps streamline procurement for these projects with discounted pricing, real-time supplier access, and tools to scale your electrification business.
The HVAC market is shifting toward energy-efficient, eco-friendly solutions like heat pumps, air quality products, and smart controls—and contractors need to adapt. To stay competitive, it’s time to modernize your procurement process and build relationships with innovative suppliers offering these in-demand technologies. Customers are increasingly focused on energy use, indoor air quality, and long-term ROI. Raiven helps HVAC professionals access cutting-edge products, streamline sourcing, and stay ahead of market trends.
The new LEED v5 standard—and similar building certification programs—are making sustainable upgrades more data-driven, measurable, and rewarding. These frameworks create clear ROI for building owners while opening up new opportunities for HVAC and electrical contractors. From retrofits to smart sensors, there’s growing demand for experts who can plan, source, and install energy-efficient solutions. Raiven helps contractors stay competitive in this evolving market with easy access to high-performance products and streamlined procurement tools.